Stay cool, Stay Secure: Buffer Tank Solutions
Uninterrupted Cooling
Stable Temperatures
Perfect for Data Centre
Why Choose Us
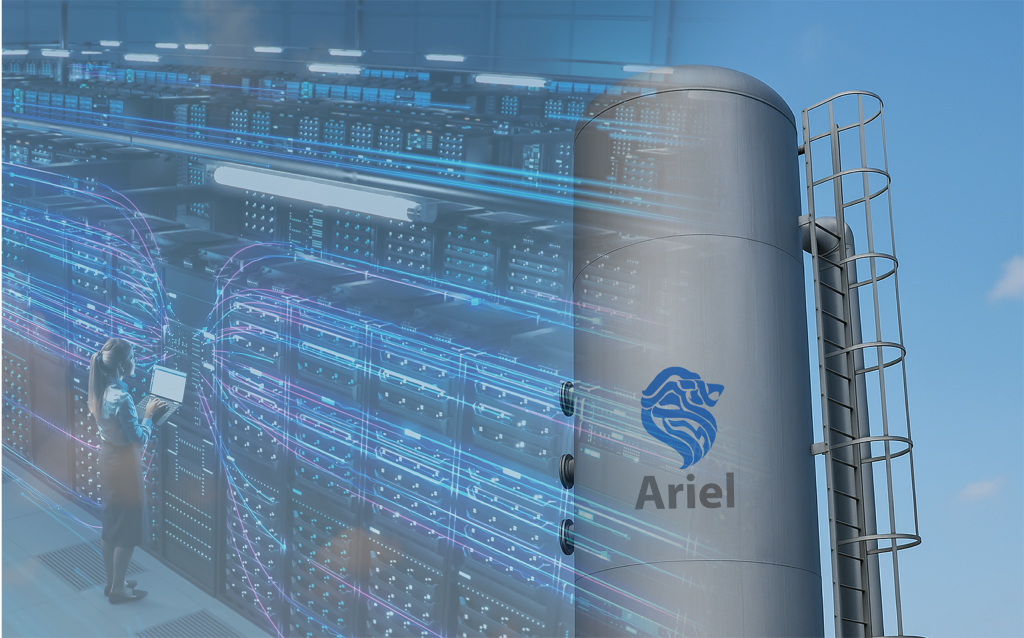
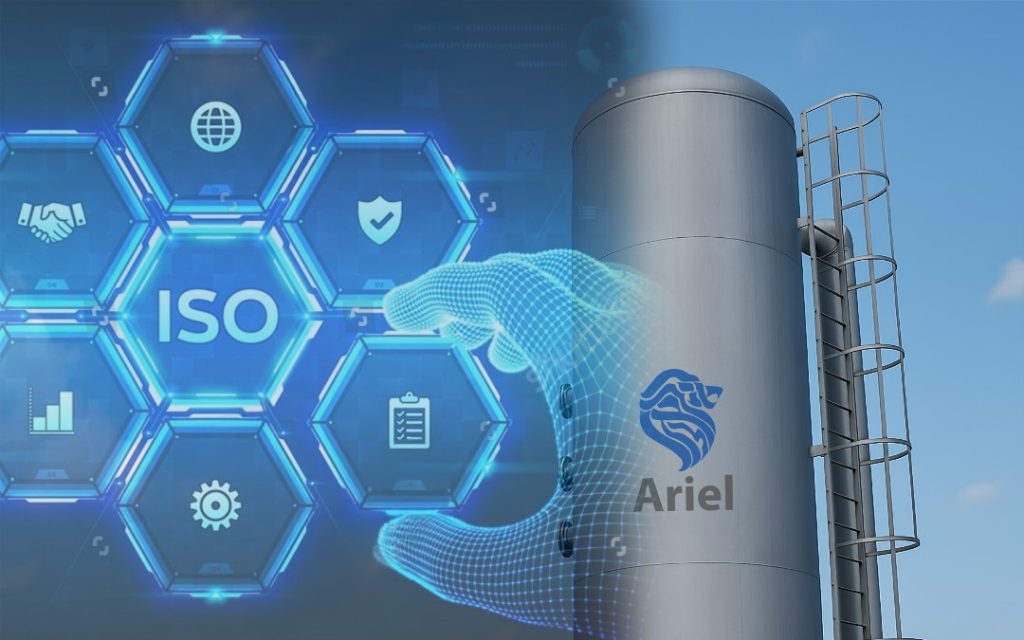
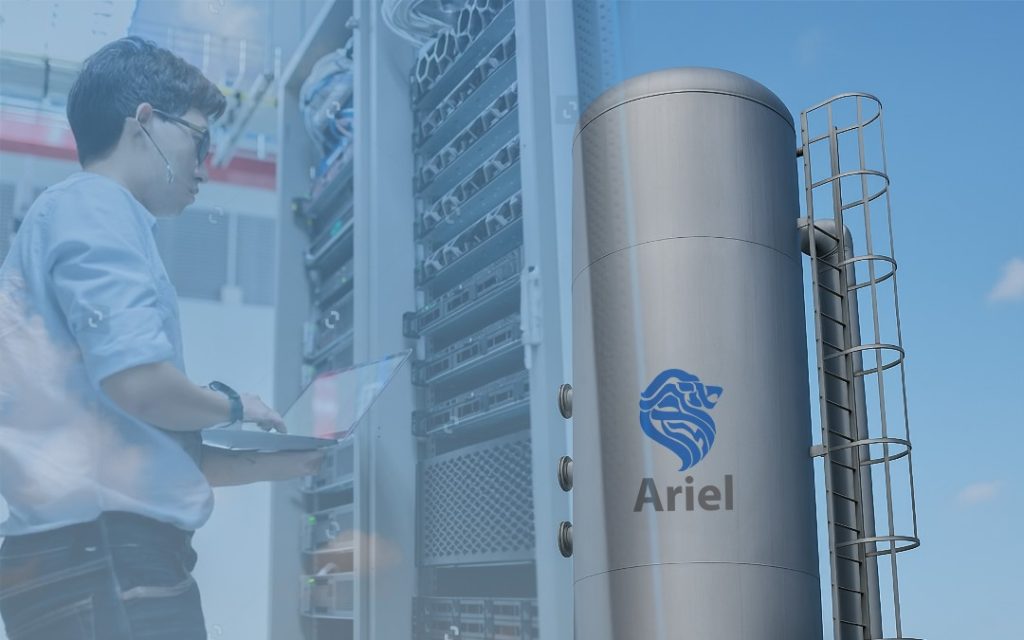
Reliability Engineered
In data centers, buffer tanks:
– Stabilize chilled water temperature and flow for IT equipment.
– Provide emergency buffers during power outages.
– Ensure Tier III/IV uptime compliance
Certified Resilience
– Our tanks are built to ASME SECT.VIII DIV.1 (2023 Ed.) for safety standards.
– Ashrae Guideline-compliant design
– ISO 9001 certified manufacturing.
Performance Assured
– Maintains ±0.5°C chilled water temperature stability, like holding 14°C for 5 minutes.
– 5-year warranty + 2-year performance guarantee.
– validated by CFD modeling for reliable performance. Low pressure drop design.
Buffer Tanks Engineering Schematics
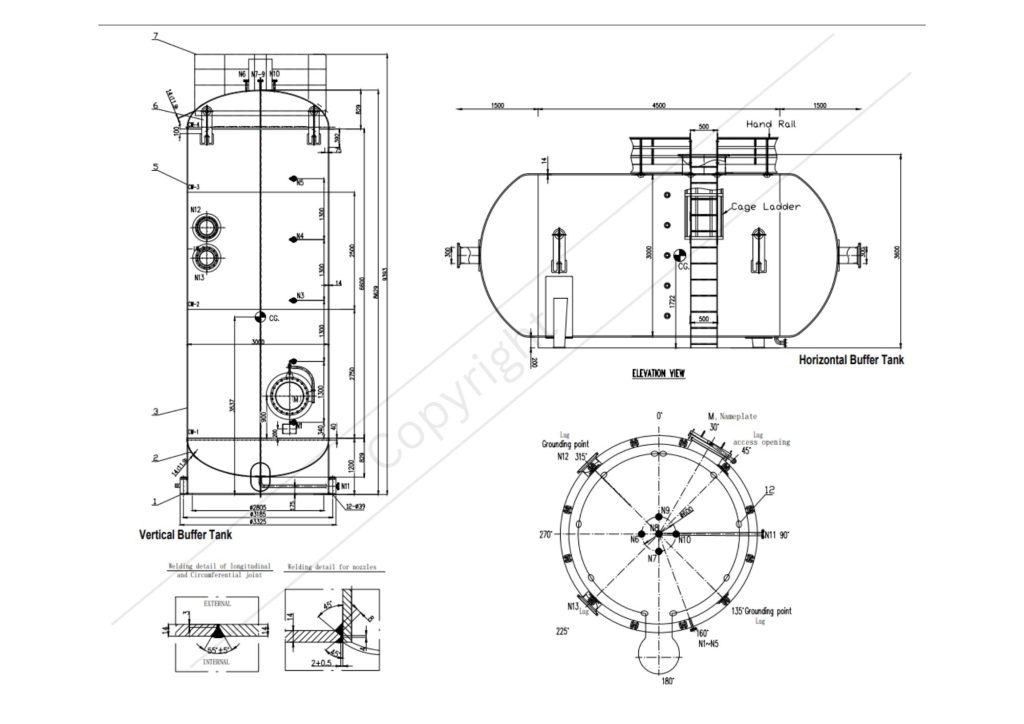
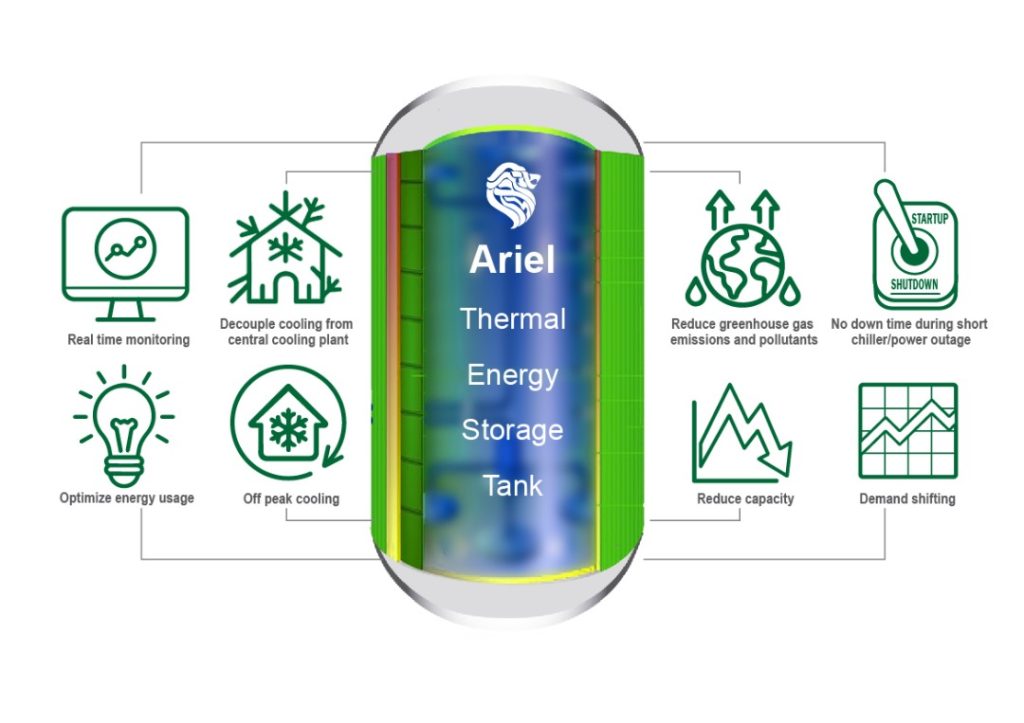
Real time monitoring
Enables predictive maintenance, smarter decision-making, and faster response times.
Reduce System Capacity
Reduce the size of chillers needed because the tank stores extra thermal energy.
Optimize Energy Usage
Using stored energy to handle fluctuations in demand without ramping up equipment unnecessarily by protecting the chiller.
Off-Peak Cooling
Helps avoid peak-time electricity charges and eases load on power infrastructure.
Decoupling Cooling from generation, Central Cooling Plant
Cooling delivery even when the central plant is off or idle.
No Downtime During Short Chiller or Power Outages
The buffer tank continues to supply cold water, preventing system shutdown.
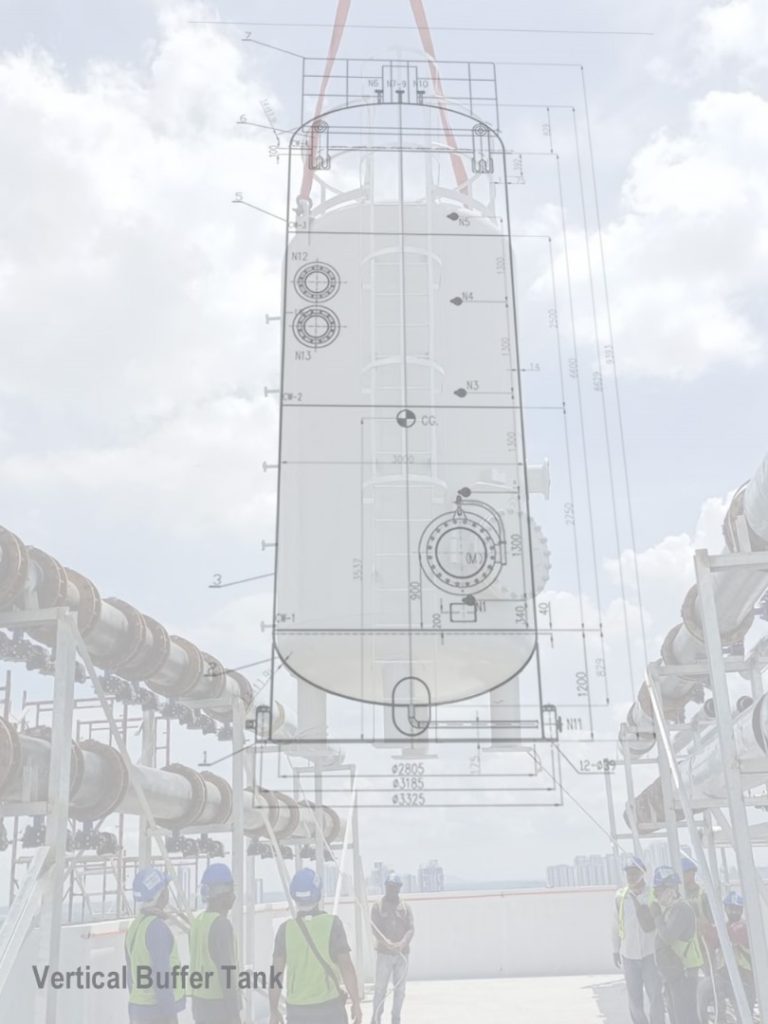
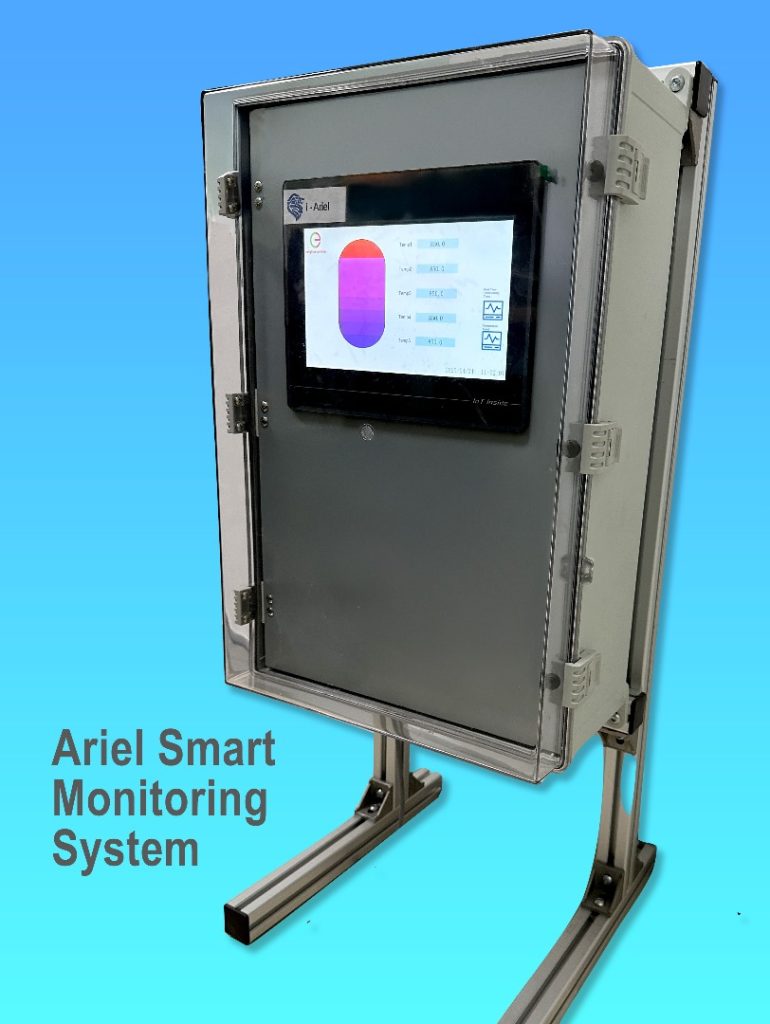
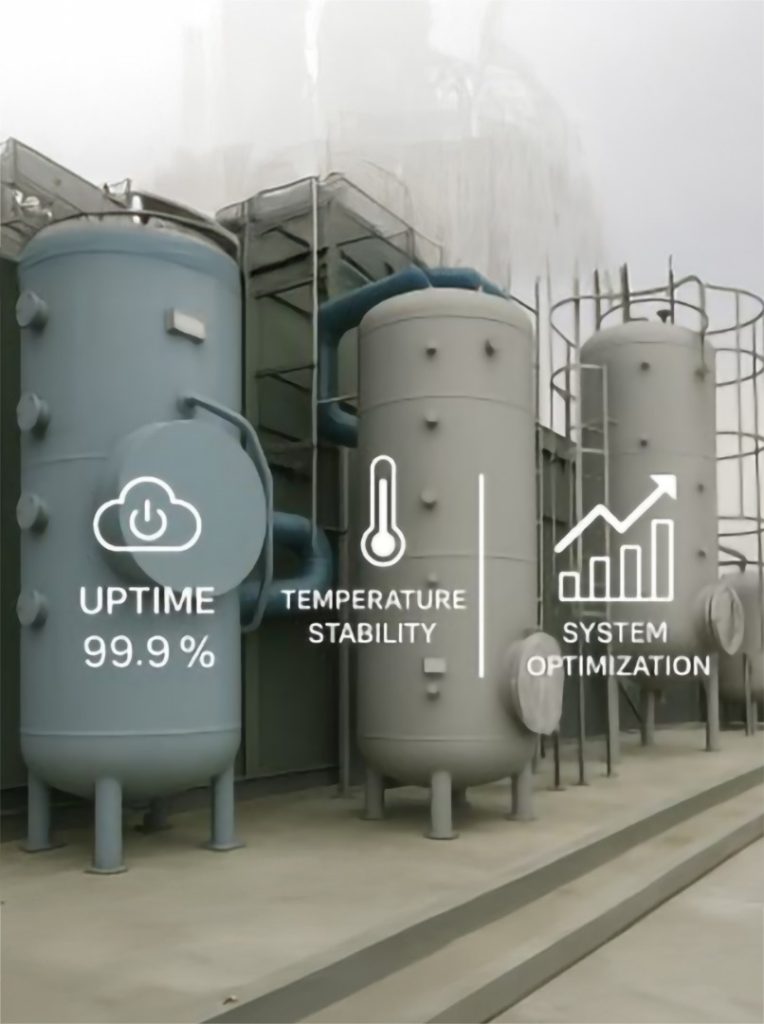
Customizable Solutions
We offer customizable vertical & horizontal buffer tank with various sizes and specifications to meet the unique requirements of your industry. Contact us for details.
Smart Monitoring
Our Smart Monitoring system provides real-time temperature visualization, enabling proactive maintenance and system optimization.
Stable Temperature Control
ARIEL buffer tank stabilize temperature of chilled water supply, preventing temperature fluctuations and optimizing cooling system performance.